The home of Tambayaki,
where handwoven history
and tradition come alive
Tambayaki potters and their families continue to build upon 850 years of history and knowledge
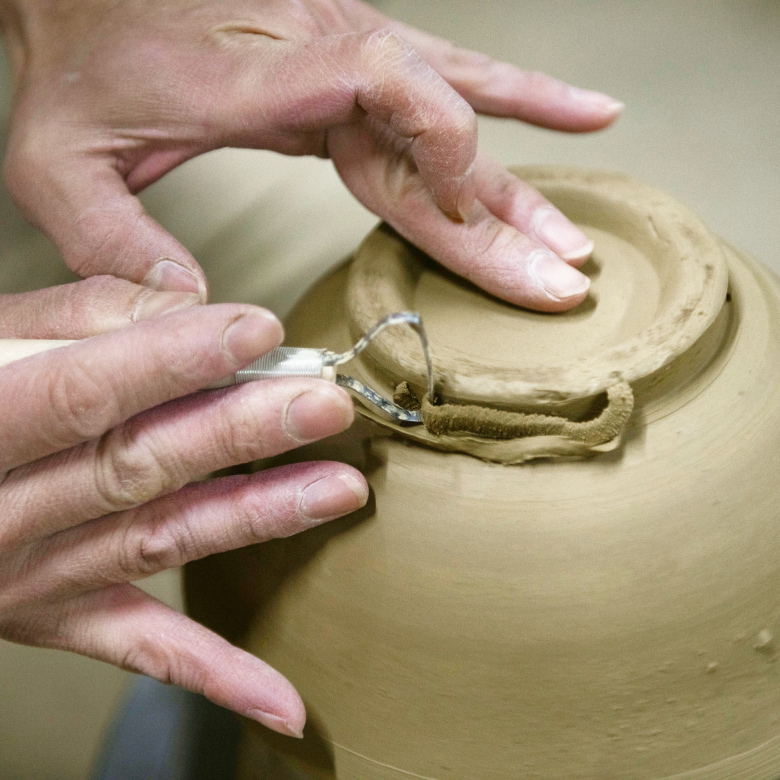
The fires of the kilns of Tachikui have been kept burning for dozens of generations and, even today, there are nearly 60 small, family-run kilns that are dedicated to making pottery.
The people of Tachikui, who have peddled their wares throughout Japan, welcome visitors with the strength and friendliness of people who have carved out their own livelihoods without wholesalers.
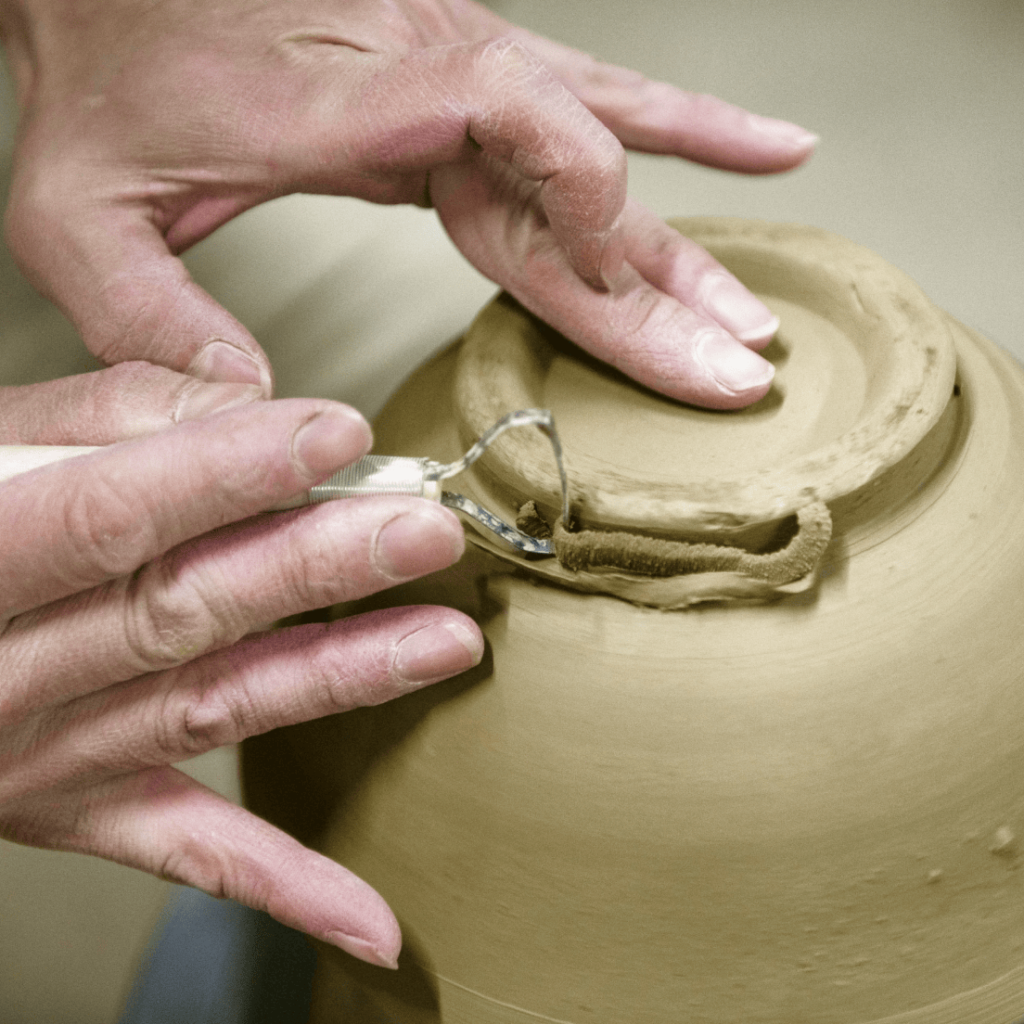
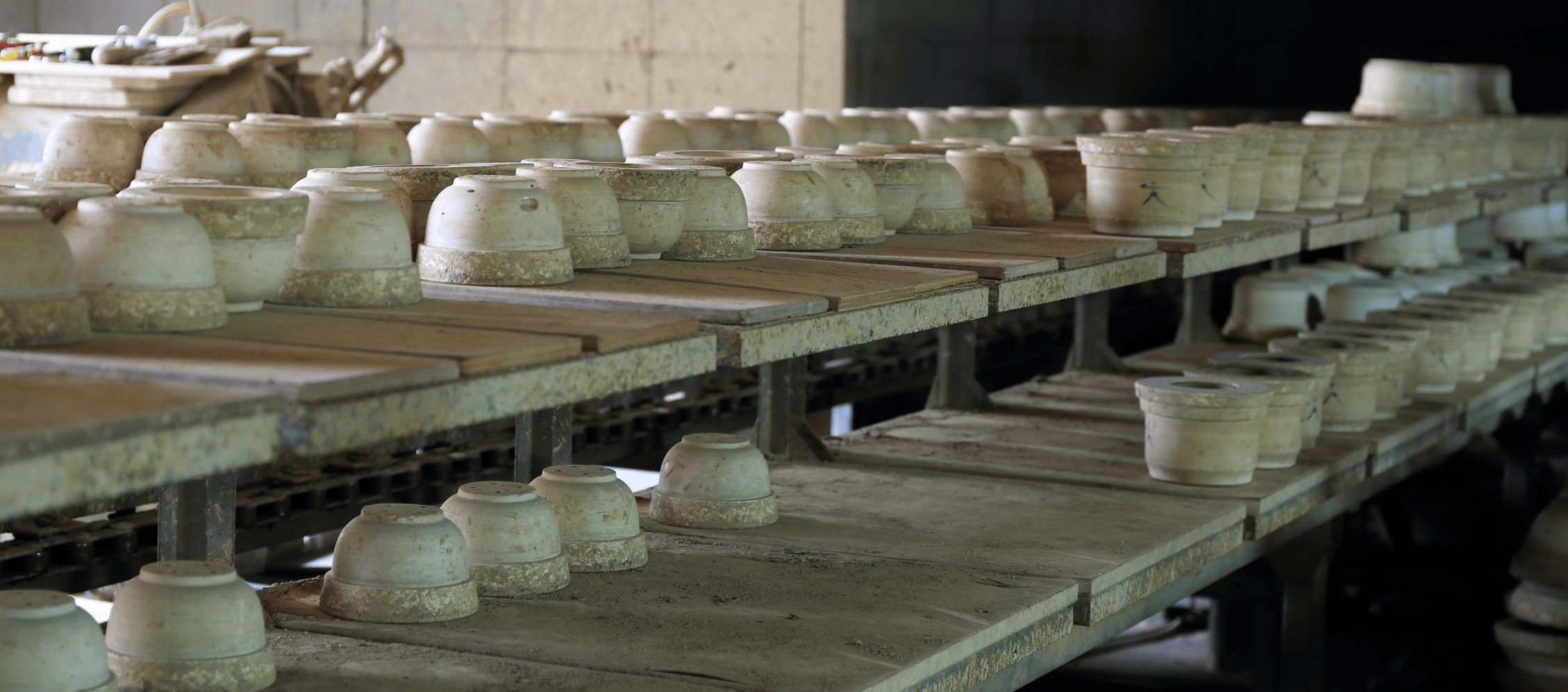
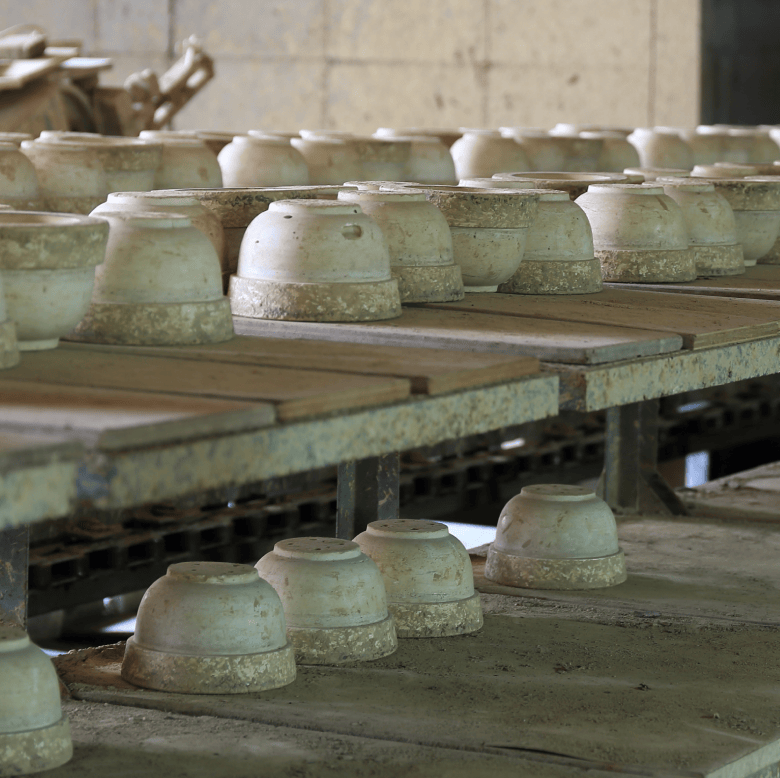
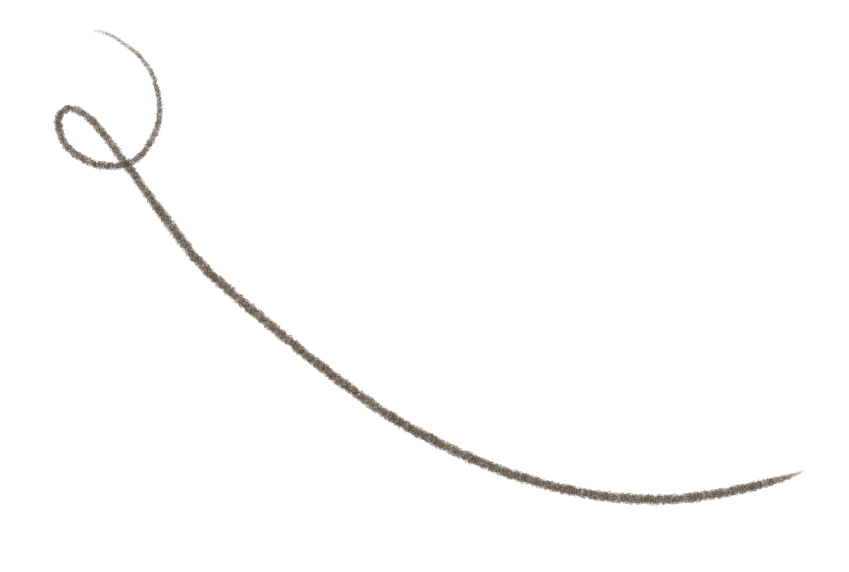
The noborigama kiln, the ‘climbing kiln’, is a symbol of Tambayaki and is said to have once been over 100m long. During the Edo period, noborigama kilns were jointly managed by several potters, who fired pots, jars, mortars, and other daily utensils in response to the needs of users.
Today, Tambayaki’s appeal lies in the strong solidarity of the pottery cooperatives, which still collectively refine the clay and operate their own sales locations. This has resulted in diverse aesthetic sensibilities which are nurtured through encouraging the freedom and open creativity of the individual artists.
Attracted by this appeal, many young makers are able to follow in their parents’ footsteps whilst also finding their own creative voice and forging a bright future for the production area.
It is precisely because of this freedom and creativity that the spirit of handicraft that is being passed down is alive and well in Tachikui.
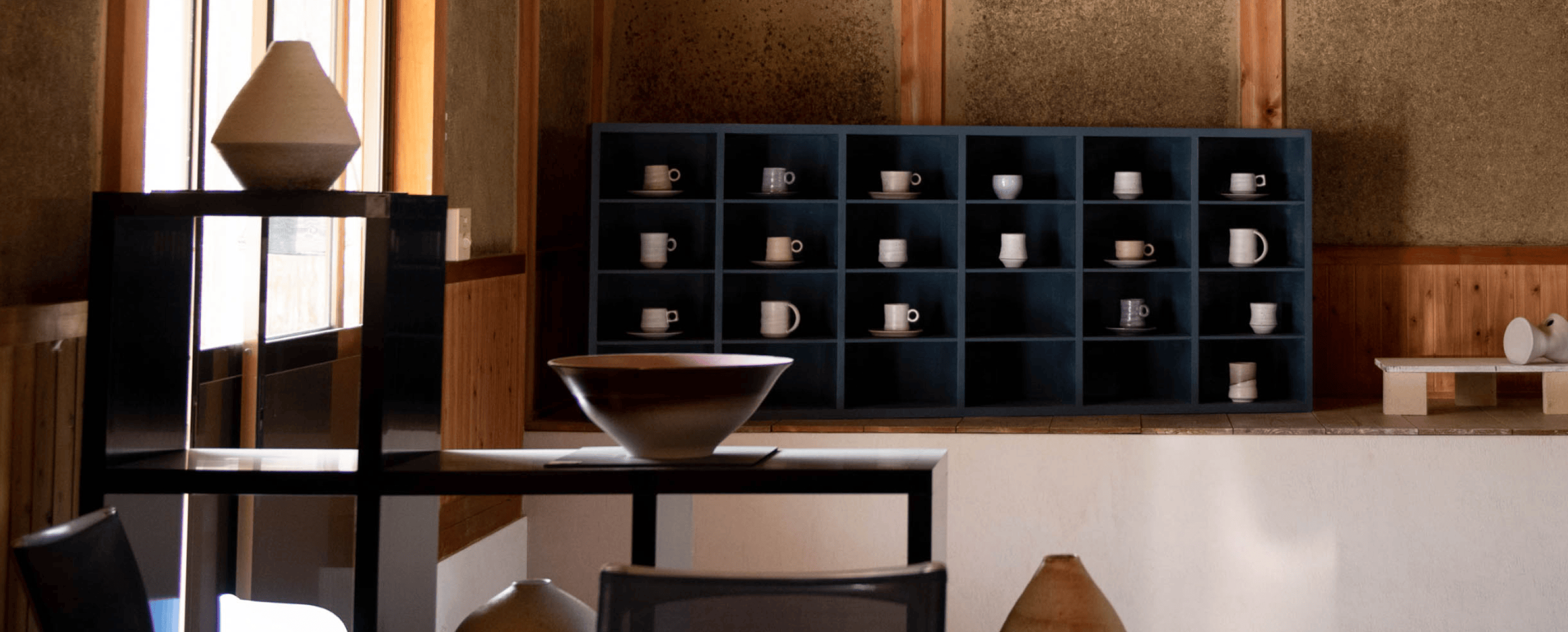
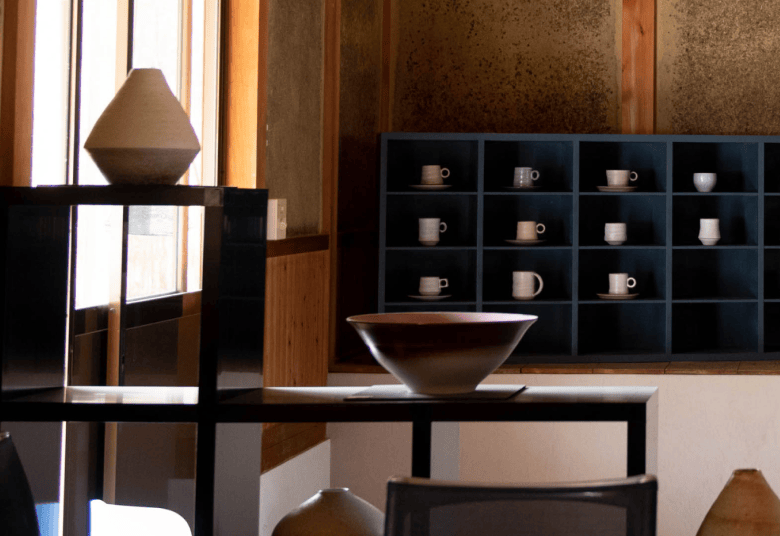
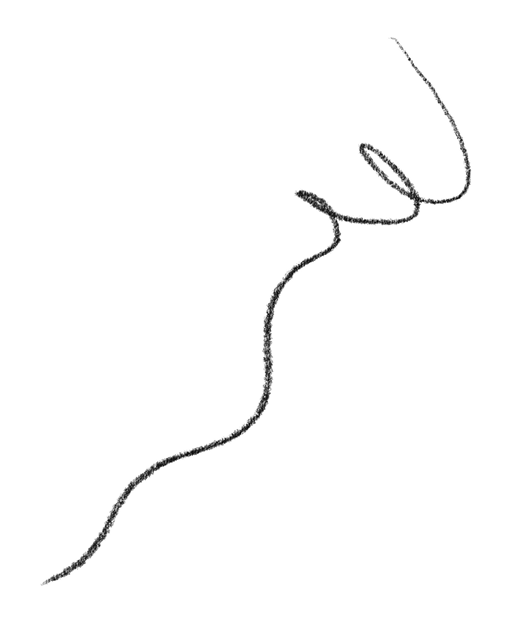
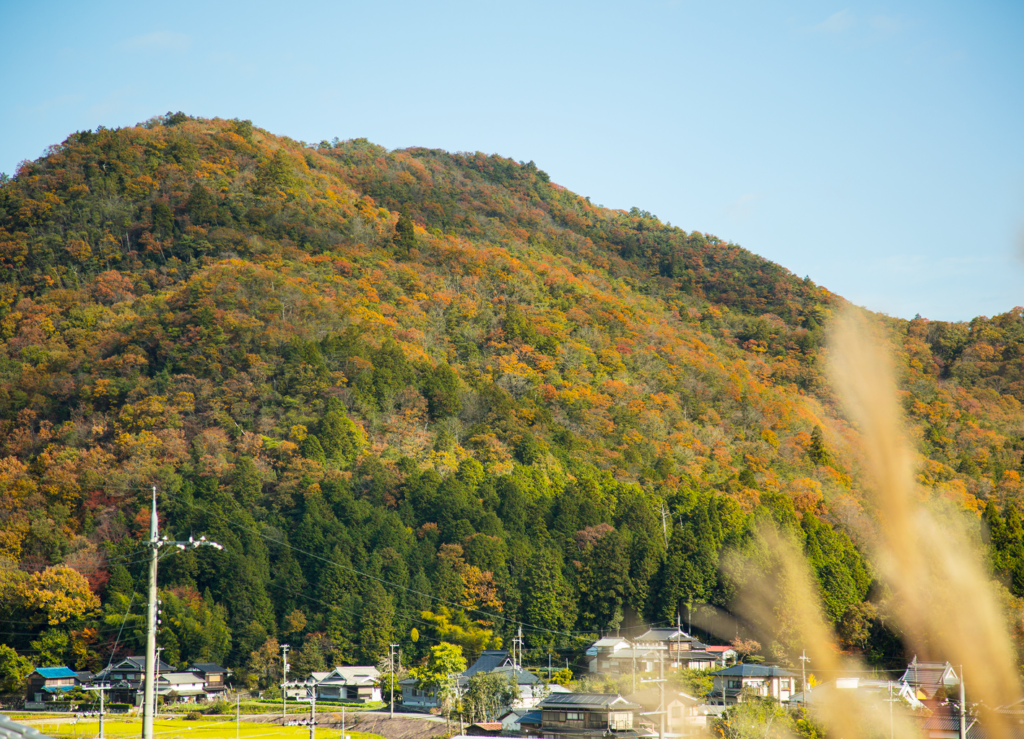
The climate in which Tambayaki is born
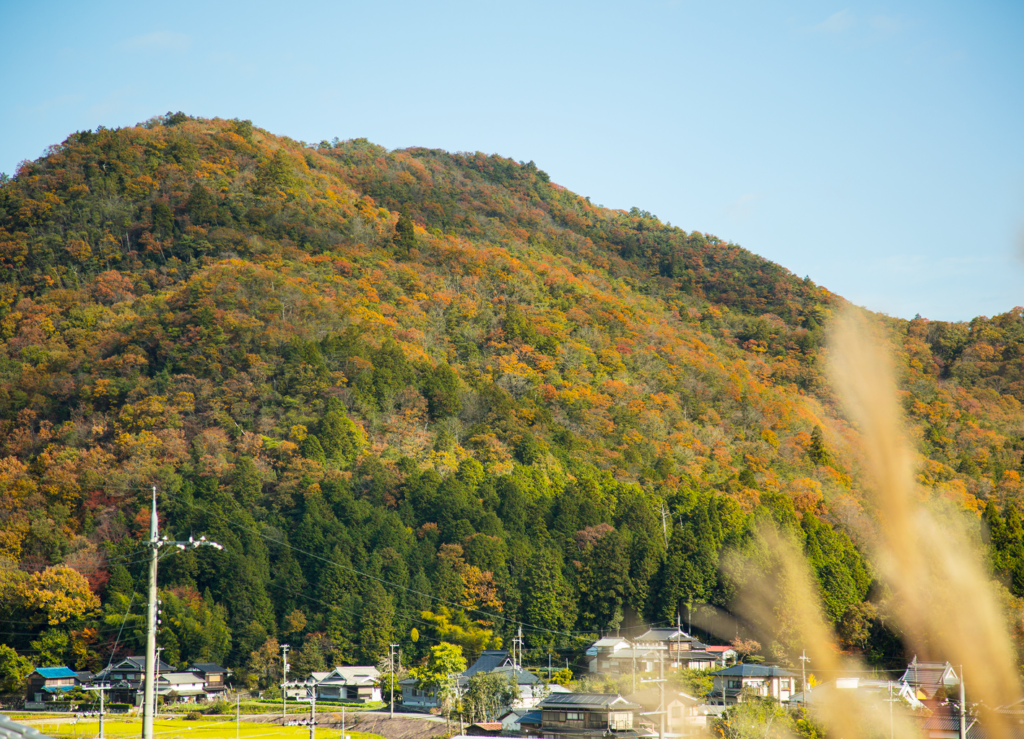
Tachikui is a mountainous area with abundant nature, which produces red clay suitable for use in pottery. The clay that is being used today is mountain clay and paddy clay.
Good historical access to transport via rivers and overland routes, as well as Tachikui’s proximity to large cities such as Kyoto, Osaka and Kobe, have contributed to the continued operation and passing down of knowledge in this pottery production region.
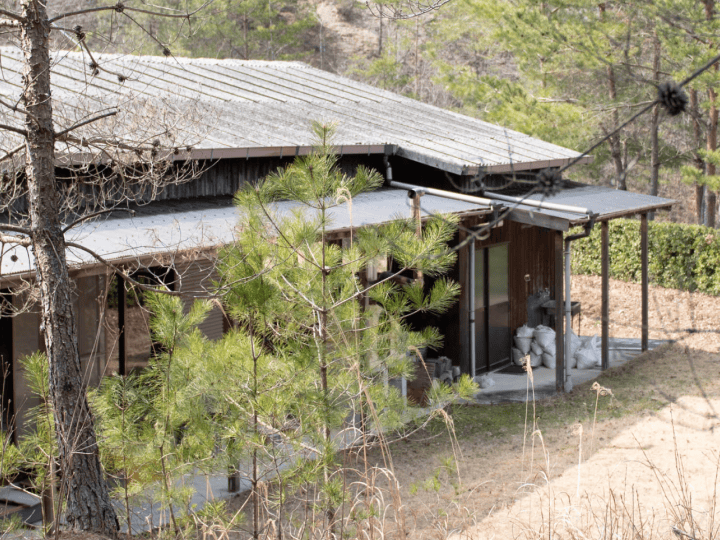
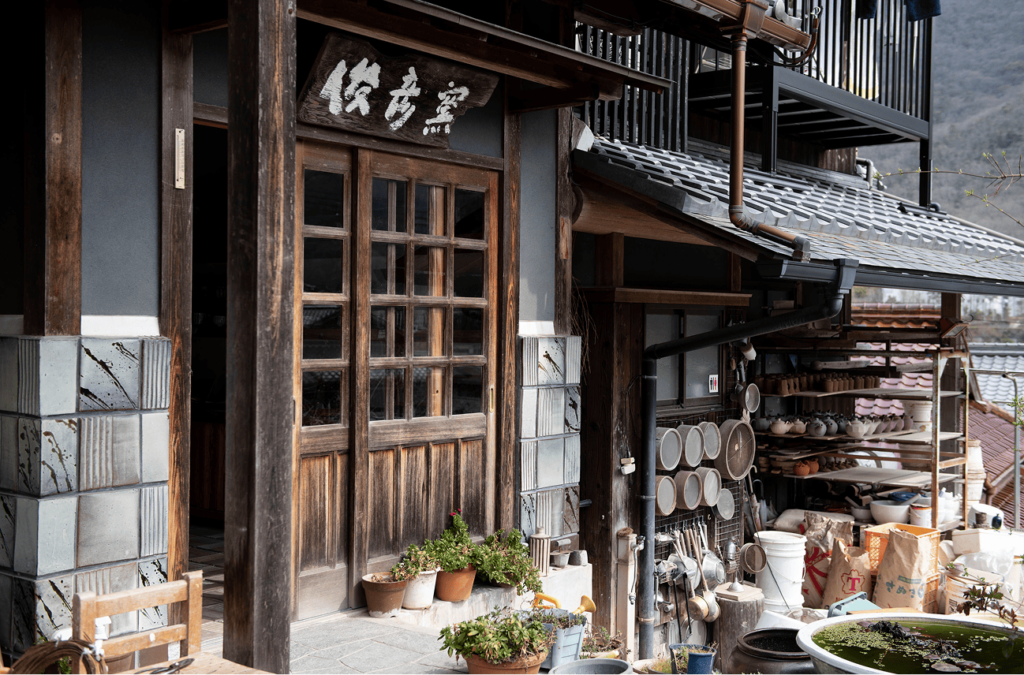
Walking through the side streets of Tachikui, you can enjoy the typical scene of creations drying in front of houses before they are fired, pots filled with naturally occurring glazes and haphazardly scattered plaster molds. If you are lucky, you may be able to spot a wisp of smoke rising from anagama or noborigama kilns that are being fired.
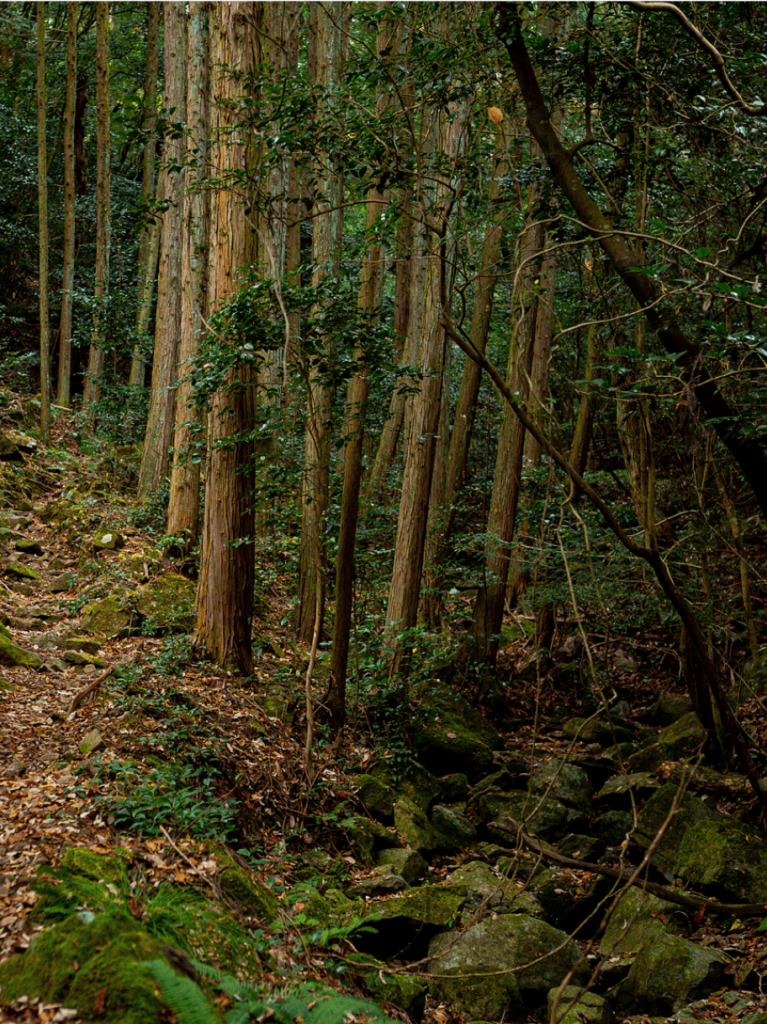
Nestled between Mount Kokuzo and Mount Wadenji, this valley village is a place where you can see vibrant greenery in spring, dancing fireflies in summer, colorful leaves in autumn, and enjoy pleasantly crisp air and warm fireplaces in winter. In Tachikui, you can encounter different views every single day.
Tamba pottery is born by facing the clay and collaborating with earth and fire in the midst of such a richly delightful and simple village life.
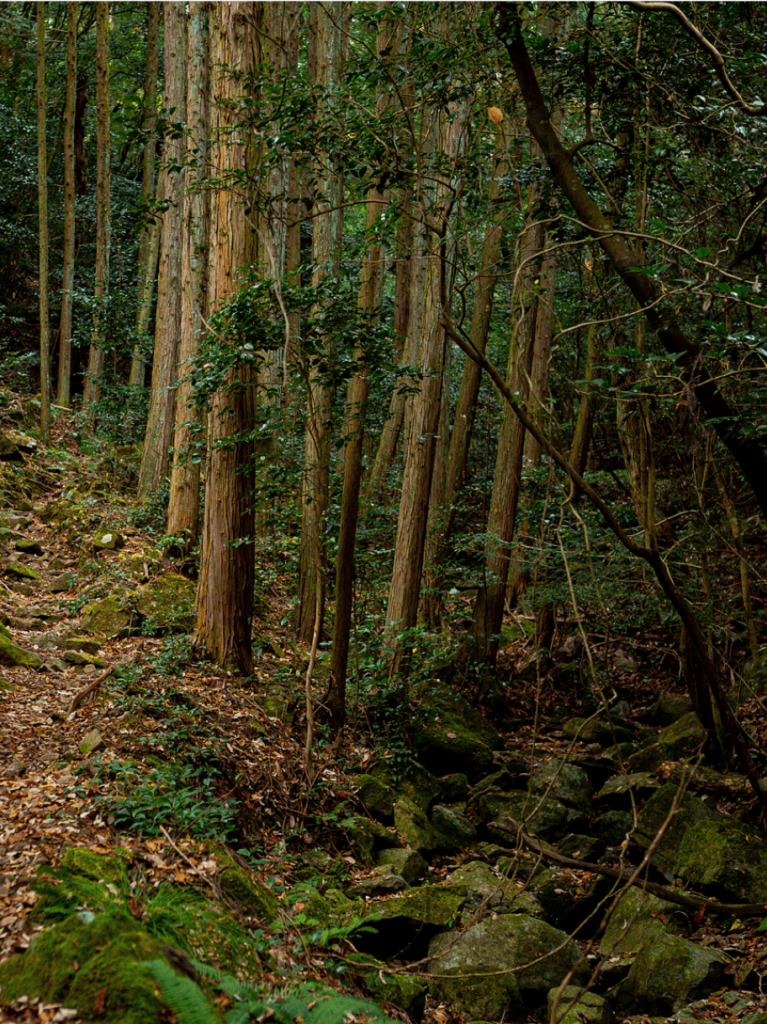
The process of creating Tambayaki
Pottery clay, the raw material for pottery, is produced at the earthenware factory of the Tamba Tachukui Pottery Cooperative. However, there are also some potters who take natural clay and refine it themselves.
The creation of pottery begins with the careful kneading of the clay, removing the air while ensuring an even distribution of particles and water.
Next, the clay is shaped using a potter’s wheel or plaster mold. Skilled Tambayaki potters can instantly transform the clay into a variety of shapes, including vessels, cups, sake cups, flowerpots, and vases, breathing new life into the clay. While still damp, the clay is scraped and finished with a bamboo or iron plane.
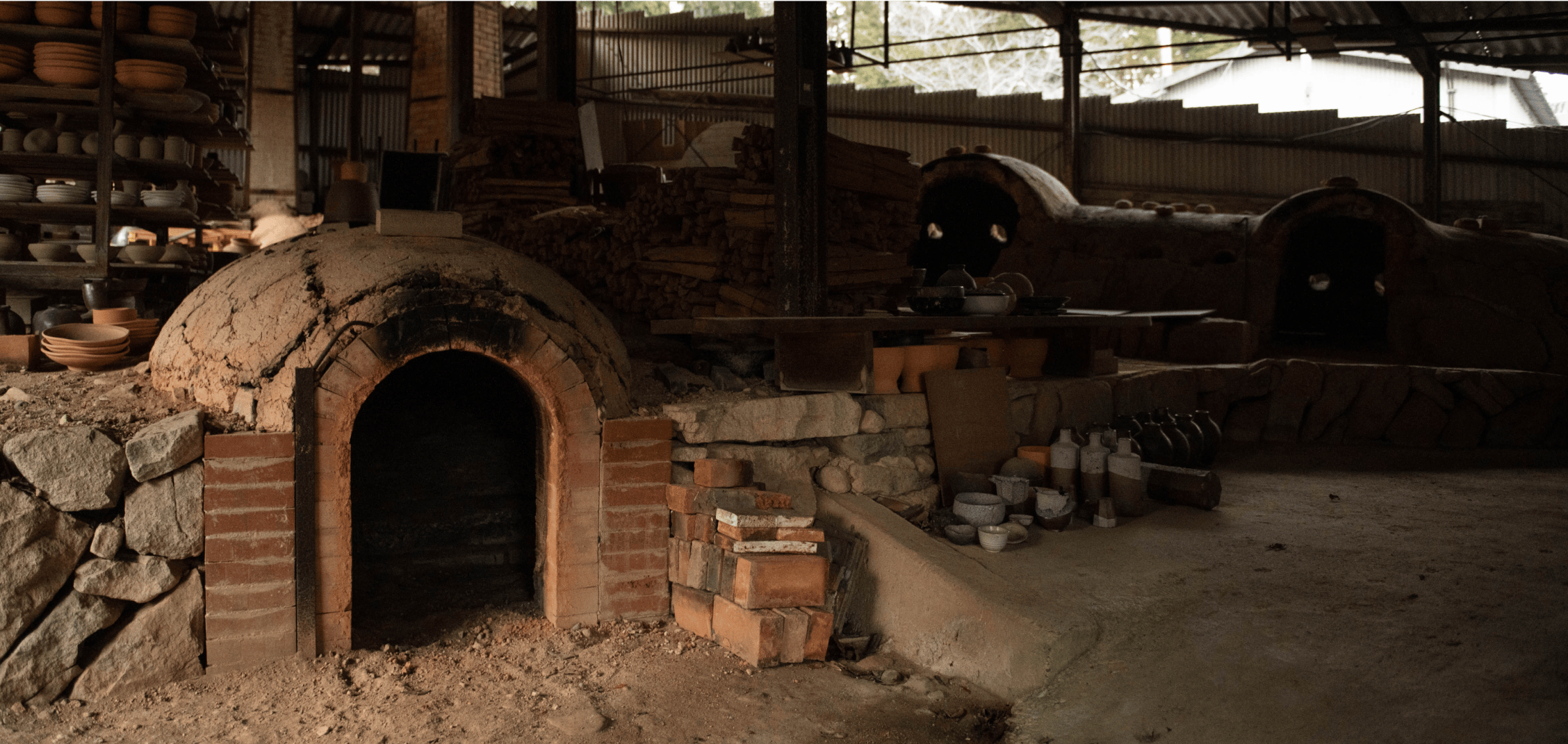
After drying, the creations are either left unglazed, or have glazes (such as ash and iron glazes) applied to them, before finally being finished by firing at a temperature exceeding 1,200℃. If a noborigama kiln is used, the fire is kept burning for three days and three nights with wood.
The entire process is carried out in a natural environment that is affected by weather, temperature, and humidity. The patterns on pottery created by the flames of a noborigama kiln can be said to be a collaboration between the maker, the earth, the sun, the wood and the wind.
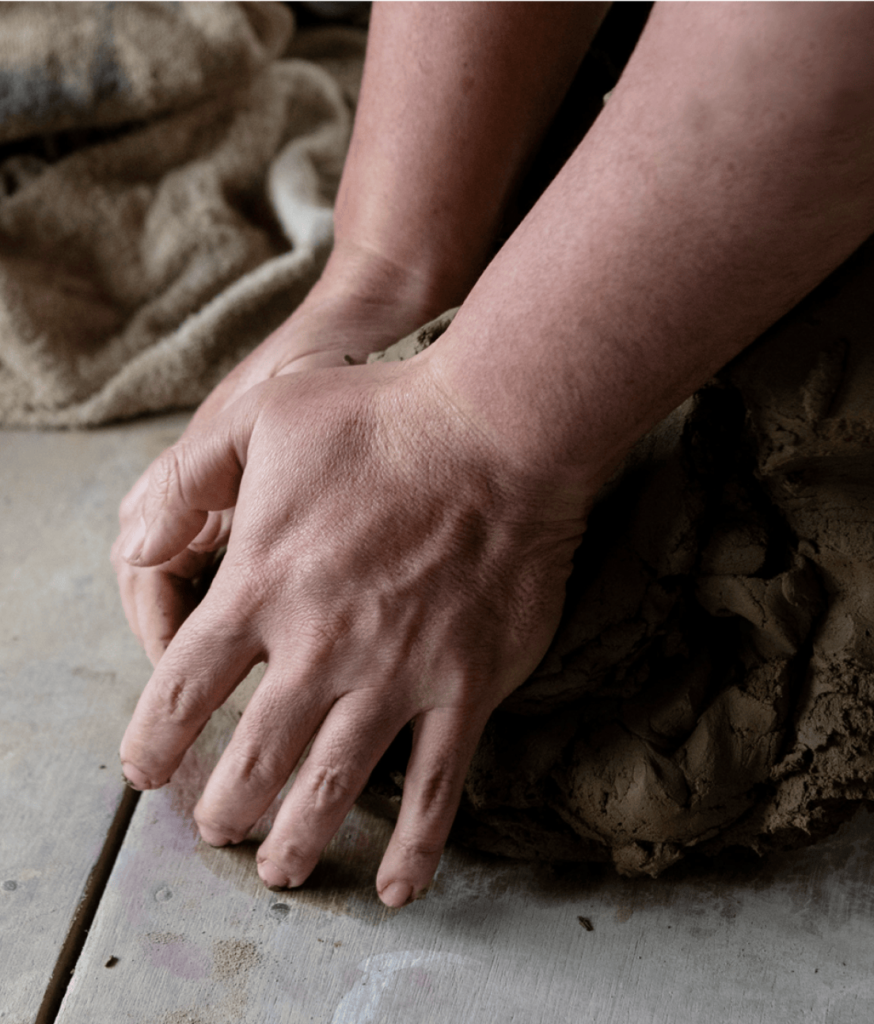
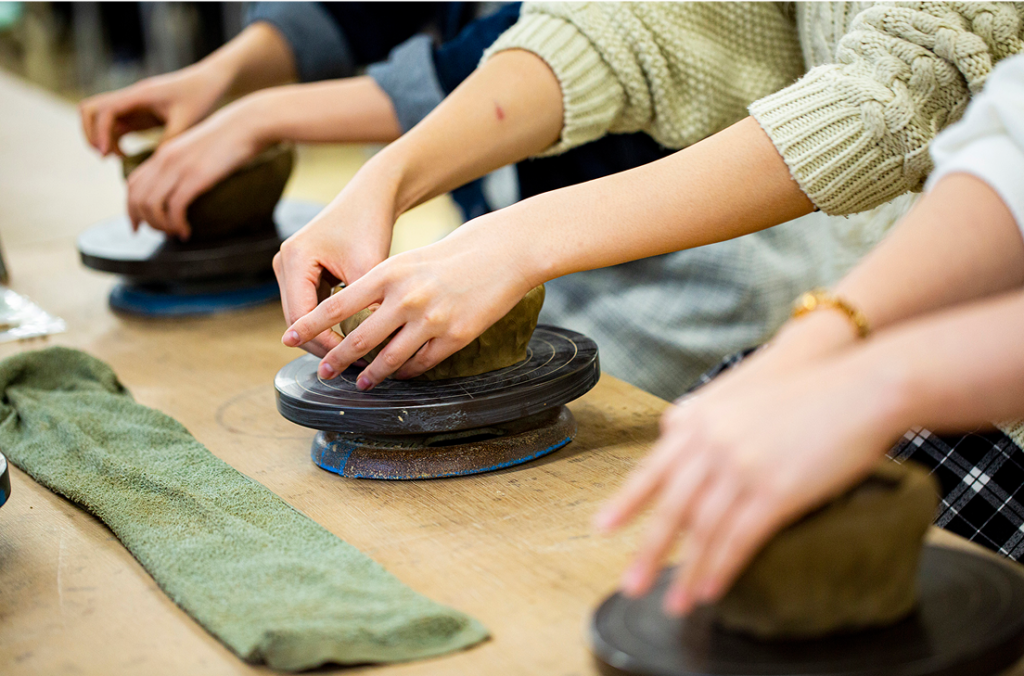
Pottery Experiences
Why not experience the creativity of traditional handicrafts through pottery experiences in Tachikui, a place with 850 years of Tambayaki history? Here, you can enjoy shaping and painting your own pottery under the guidance of an instructor. Your creations will be carefully fired and finished by a local potter.
Under renovation
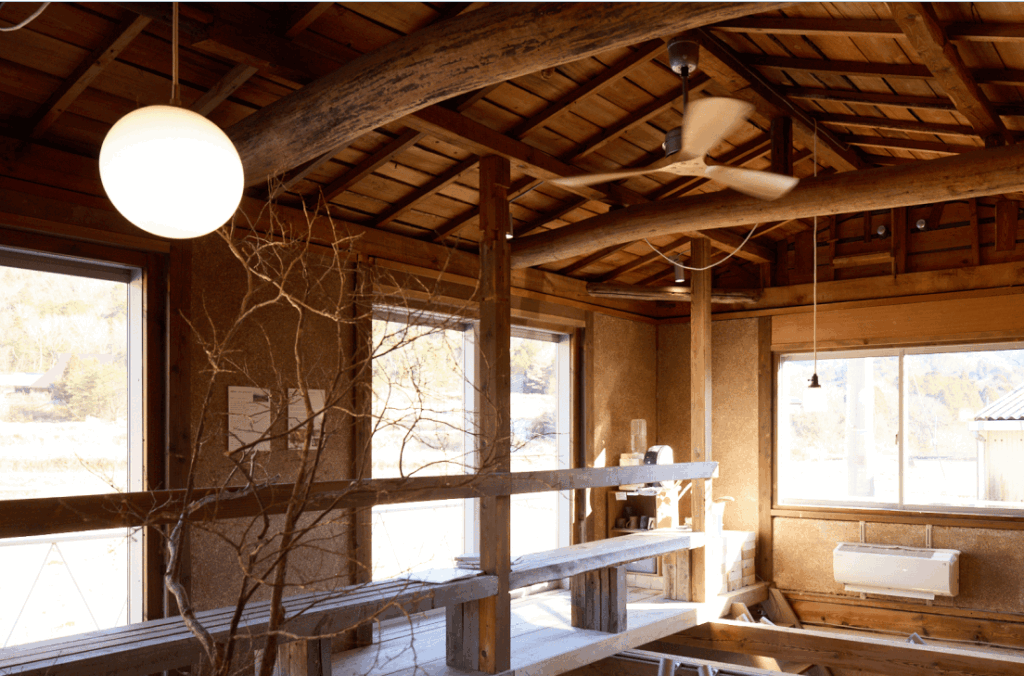
Pottery Stays (TAMBA TOHAKU)
Pottery Stays (TAMBA TOHAKU) is a special experience that allows you to deeply appreciate the charm of Tambayaki while staying in accommodation surrounded by the beautiful nature of Tachikui. By coming into contact with the lives of local potters and sharing meals together with them, you can feel the breath of traditions that have been passed down from generation to generation, and ponder upon the profound world of traditional handicrafts.